1 前言
电泳涂装线有很多水洗工艺,也是大量使用水、消耗水的工艺过程。随着我国大范围内水资源的短缺和建设节约型社会的需要,以及环保、污水排放等法规日益受到重视,污水处理费用也日渐上升,电泳涂装线如何合理制定水洗工艺,在保证工件清洗质量的前提下合理使用水,**大程度地降低水的消耗和污水排放,提高水的利用率,是一个越来越受到重视的问题。
2 电泳涂装的水洗
电泳涂装线常规的工艺设计为:预清洗(喷淋)→预脱脂→脱脂→水洗(喷淋)→水洗(浸渍)→表调→磷化→水洗(喷淋)→水洗(浸渍)→循环纯水洗(喷淋)→纯水洗(浸渍)→干净纯水喷淋→电泳→0次喷淋→循环超滤水洗1→循环超滤水洗2→循环超滤水洗3→干净超滤液清洗(喷淋)→纯水洗→干净纯水喷淋。在电泳涂装中,主要的水洗工艺为脱脂前后、磷化后、电泳后的各道水(超滤液)洗。在实际涂装线上,由于工件形状、要求或设备投资因素各不相同,各水洗工艺的水洗工序个数、工作方式可能有所不同,有喷淋、浸渍,或喷浸结合。
2.1 脱脂前、后的水洗
2.1.1工艺说明
预清洗工序一般采用大流量的喷淋方式,也称“洪流清洗(flood)”。预清洗槽用来冲洗复喷的工件、新脱除涂层后的挂具(为了保证良好的导电性)、久置的落满灰尘毛絮的工件等,同时除去工件上所带的焊渣、颗粒等,以降低脱脂槽的污染程度,减轻后续工序的过滤负荷及过滤袋的更换频次,并防止喷淋管道喷嘴的结垢堵塞。预冲洗槽的水位保持极低,能维持水的循环即可,因悬挂不牢固冲落的工件可以及时从预冲洗槽中拣出。此工序在以前的电泳涂装线设计中一般没有,但是近几年涂装水平发展的需求,已越来越多地在新建涂装线中设置。从实际使用情况看,对电泳涂装质量的提高、设备的管理等均带来较多的好处。在有的汽车涂装线上,甚**在上线前还有人工用高压水枪以约0.6MPa的压力对工件进行冲洗。
(2)脱脂后的水洗工序
主要是清洗干净工件表面、内腔等所携带的脱脂液及其它杂质,防止工件带液串槽,污染下道工序,影响处理质量。一般脱脂后有1道或2道水洗,可以采用喷淋,也可以采用浸渍(如果仅有l道洗,要求用浸渍水)。在设计中,值得注意的是,脱脂后的工件到水洗的间隔时间不可太长,也就是说在进入水洗工序前,既要保证工件有充分沥液时问,也要保证脱脂后工件表面不能出现大面积的干燥现象。工件水洗后到进入下道工序之问的间隔时间也不可太长,防止工件出现返锈现象,影响后续处理质量。另外,水洗槽的设计底部应有倾斜角,或者其它设计形式,以保证少量沉淀汇聚到底部排污管口,利于清槽洗槽。现在大多数汽车涂装线已在水洗循环管路上安装过滤器,有的汽车涂装线还加装旋风式分离器和磁性过滤器,可以捕捉95%的20mm以上的铁粉颗粒物,可以大幅度减少工件涂层表面的颗粒、灰粒等弊病。同时有助于清洗后的工件在出水洗槽后没有异物附着、二次污染等状况。
2.1.2 用水的管理
工件的清洗质量如何,除了设备因素外,与清洗用水的水质也有很大关系。为了提高清洗质量,需要对清洗水不断地更换、更新,因此也是用水及排水的重要部分。
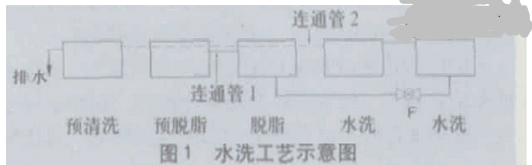
如图1所示,要做到合理用水一般在预脱脂槽、脱脂槽之间有连通管l外,在预清洗和水洗槽间增加连通管2,并保持水洗槽的液面高于预冲洗槽的液面。在水洗槽循环管路上增加一个引水支管,通过阀门F控制,可以将水洗槽内的水加到脱脂槽内。仅在**后一道水洗槽配备自来水加水管,撤消其它槽上的自来水加水口。通过阀门控制可以用水洗槽内的水补充脱脂槽,或经脱脂槽补充到预脱脂槽(脱脂槽液因高温蒸发和工件消耗携带而减少),也可以用来配制脱脂槽溶液,冲洗预脱脂槽和脱脂槽。日常靠水位高度差通过连通管2补充预清洗槽所需要的清洗水,并经预清洗槽排放,完成水的多重循环利用。
2.2 磷化后的水洗
2.2.1 水洗工艺
磷化后的水洗主要是为了清洗干净工件表面、内腔所带有的磷化液、磷化渣、金属离子及其它杂质离等,同时保证工件清洗后的滴水电导率满足
电泳槽对入槽工件的要求,防止对
电泳槽液带来污染。工件清洗的效果直接影响到电泳涂装的质量和
电泳槽液的稳定性。磷化后的水洗一般有自来水喷淋清洗、自来水浸渍清洗、纯水浸渍清洗、纯水喷淋洗、干净纯水喷淋清洗等各道工序。
在设计中,一般工件出磷化槽后会有磷化液的喷淋管路,用以初步清洗工件表面的磷化渣,这点在实际使用中证明是能起到比较好的效果的。磷化后的**道水洗一般设计为喷淋方式工作,达样,槽体体积一般比较小,以方便更新水洗水,提高清洗效果。在设计中,也应注意工件在进入电泳槽前,外表面不要出现半干半湿的情况,以免产生漆膜弊病。如果出现此类问题,建议在入槽前增加工件的增湿或吹千工序及其设备。对丁各水洗槽,建议也安装过滤装置。对防止工件上吸附磷化渣,避免工件表面出现颗粒、灰粒等有很多好处。#p#分页标题#e#
2.2.2 用水的管理
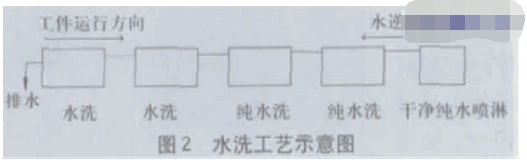
从图2可以看到,磷化后到电泳前的水洗工艺,各槽均有连通管,应采用逆向补水的方式,提高水的利用率。干净纯水喷淋工件后,清洗水回到纯水洗槽,纯水洗槽水溢流到前面自来水洗槽,然后再溢流到前面自来水喷淋水槽,通过喷淋水槽排放,实现水的重复利用。通过检测各槽水的pH值、电导率等控制清洗水的排放和更换。日常生产管理中,在需要全部更换纯水洗槽时,可以用纯水洗槽的水置换自来水洗槽,或者在更换自来水洗槽时,用纯水槽里的水冲洗自来水槽。
2.3 电泳后的水洗
电泳后水洗主要清洗干净工件内外表面浮漆、夹层内的漆液,提高漆膜外观质量,回收漆液,提高漆液的利用率。工件从电泳槽不可避免地会带出部分漆液,这部分涂料如果经水洗后作为废水直接排放,既加重了废水处理的负荷,亦大大降低水涂料利用率,相应增加了涂装成本。而利用超滤液作为水洗水,可实现封闭式循环清洗,提高涂料利用率,减少废水排放量,节约纯水用量。
电泳后水洗系统从工艺选择上可以有多级选择,从理论上说,超滤水洗段数越多,涂料回收效率就越高。但是,实际生产中并非超滤水洗段数越多越好。因为每增加一级超滤水洗,设备长度、设备投资成本及运行成本均随之提高,而涂料回收效率的提高却是有限的,在设计超滤水洗级数时,应综合考虑几个方面的因素,通常选用三级超滤水洗即可达到满意的效果。
如图3所示,在布置涂装线电泳后的水洗工序时,大都采用喷洗和浸洗相结合的方式,而且比较多的采用由2级喷洗和l级浸洗组成的3级循环水洗和l级干净水洗。由于3级循环水洗有3种布置方式,即喷—浸—喷、浸—喷—喷和喷—喷—浸。根据Ted Mooney理论计算,要达到相同的清洗效果,耗水量与采用的工作布置方式无关。但从实际情况看,只要工件上附带的杂质经过较长时间而不**于变得难于清洗,为了便于生产控制,浸洗工序应尽可能放在**后。因此,建议选用喷—喷—浸这种布置方式。
当然,工件清洗的效果和回收效率的高低还同电泳超滤设备超滤液的透过量有关,随着超滤液透过量的增加,工件的清洗效果、涂料的回收效率明显提高。但不意味着超滤液透过量越大越好。因为超滤液透过量越大,相应的超滤设备投资就越高,且当超滤液透过量增加**一定程度时,回收效率的变化趋势趋于平缓。通常保持涂料回收效率达到95%即可,而不必为片面追求极高的回收效率而增加不必要的投资。一般,超滤器透过量选择按照每平方米工件需要(1.3~1.8)L超滤液来计算。超滤水洗后,工件还需要纯水清洗,一般有纯水浸洗,再加上一道干净纯水喷淋清洗工序,也是采用逆向流动重复利用水,即干净纯水清洗工件后,返回到纯水洗槽,然后通过纯水槽溢流排出。
上述工艺,还有部分清洗水排放,但是超滤设备和专用反渗透设备组合(即EDRO)应用于电泳涂装后冲洗,组成彻底的完全闭路清洗,也越来越被广大涂装线所接受,特别是环保日益严格的今天,其应用价值越来越大。
3 结语
电泳涂装的水洗工艺与水的使用,对于提高清洗质量和节约用水、降低成本等有重要影响。通过合理制定清洗工艺、管理方法,可以改变过去水的加入靠水管的压力或人工控制,也可以改变水的用量由工艺规定按时排放等做法。通过制定清洗用水的检测指标及方法,制订合理的水质范围,并使之适应不同工件的涂装生产,在保证涂装质量的前提下可以提高水的重复利用率,节约用水,降低涂装成本。